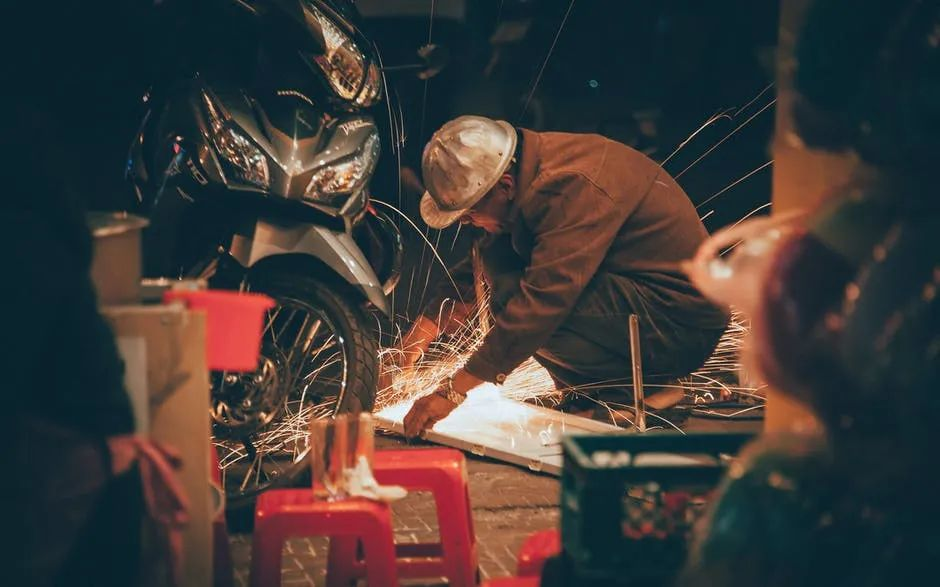
1. Genel Bakış
Rulo kaynağı bir tür direnç kaynağıdır. İş parçalarının bir bindirme bağlantısı veya alın bağlantısı oluşturacak şekilde birleştirildiği ve daha sonra iki silindir elektrot arasına yerleştirildiği bir kaynak yöntemidir. Makaralı elektrotlar kaynağa baskı yapar ve döner ve sürekli bir kaynak oluşturmak için güç sürekli veya aralıklı olarak uygulanır. Rulo kaynağı, sızdırmazlık gerektiren bağlantıların imalatında yaygın olarak kullanılır ve bazen yalıtımsız sac parçaları birleştirmek için kullanılır. Kaynaklı metal malzemenin kalınlığı genellikle 0,1-2,5 mm'dir.
Körükler vanalarda esas olarak sızdırmazlık ve izolasyon amacıyla kullanılır. İster durdurma vanası, ister kısma vanası, düzenleme vanası veya basınç düşürme vanası olsun, çeşitli körüklü vanalarda körük, vana milinin salmastrasız sızdırmazlık izolasyon elemanı olarak kullanılır. Valfin çalışması sırasında körük ve valf mili eksenel olarak yer değiştirir ve birlikte sıfırlanır. Aynı zamanda akışkanın basıncına da dayanıp sızdırmazlık sağlar. Salmastralı vanalarla karşılaştırıldığında körüklü vanalar daha yüksek güvenilirliğe ve servis ömrüne sahiptir. Bu nedenle körüklü vanalar nükleer endüstri, petrol, kimya endüstrisi, tıp, havacılık vb. alanlarda yaygın olarak kullanılmaktadır. Pratik uygulamalarda körükler genellikle flanşlar, borular ve valf gövdeleri gibi diğer bileşenlerle birlikte kaynak yapılır. Körükler, oldukça verimli ve yaygın olarak kullanılan rulo kaynakla kaynaklanır.
Firmamızın ürettiği nükleer vakum valfleri ortamın yanıcı, patlayıcı ve radyoaktif olduğu uranyum florür ortamlarında kullanılmaktadır. Körükler 0,12 mm kalınlığında 1Cr18Ni9Ti'den yapılmıştır. Valf diskine ve rakoruna rulo kaynağı ile bağlanırlar. Kaynağın belirli bir basınç altında güvenilir sızdırmazlık performansına sahip olması gerekir. Mevcut rulo kaynak ekipmanlarının üretim gereksinimlerini karşılayacak şekilde hata ayıklaması ve dönüşümü için takım tasarımı ve proses testleri yapıldı ve ideal sonuçlara ulaşıldı.
2. Rulo kaynak ekipmanı
FR-170 kapasitör enerji depolama rulo kaynak makinesi, 340μF enerji depolama kapasitör kapasitesi, 600~1 000V şarj voltajı ayar aralığı, 200~800N elektrot basınç ayar aralığı ve 170J nominal maksimum depolama ile kullanılır. . Makine, devrede sıfır kapalı şekillendirme devresi kullanarak şebeke voltajı dalgalanmalarının dezavantajlarını ortadan kaldırır ve darbe frekansının ve şarj voltajının sabit kalmasını sağlar.
3. Orijinal süreçle ilgili sorunlar
1. Kararsız kaynak işlemi. Haddeleme işlemi sırasında yüzeye çok fazla sıçrama olur ve kaynak cürufu silindir elektroduna kolayca yapışır, bu da silindirin sürekli kullanımını çok zorlaştırır.
2. Kötü çalışabilirlik. Körük elastik olduğundan, kaynak aletinin uygun şekilde konumlandırılması olmadan kaynağın sapması kolaydır ve elektrotun körüğün diğer kısımlarına dokunması kolaydır, bu da kıvılcımlara ve sıçramalara neden olur. Bir haftalık kaynak işleminden sonra kaynak uçları tutarlı olmuyor ve kaynak sızdırmazlığı gereksinimleri karşılamıyor.
3. Kötü kaynak kalitesi. Kaynak noktası girintisi çok derin, yüzey aşırı ısınıyor ve hatta kısmi yanma meydana geliyor. Oluşan kaynak kalitesi zayıf ve gaz basıncı testinin gerekliliklerini karşılayamıyor.
4. Ürün maliyetinin kısıtlanması. Nükleer valf körükleri pahalıdır. Yanma meydana gelirse körük hurdaya çıkar ve ürün maliyetleri artar.
Xinfa kaynak ekipmanı, yüksek kalite ve düşük fiyat özelliklerine sahiptir. Ayrıntılar için lütfen şu adresi ziyaret edin:Kaynak ve Kesme Üreticileri - Çin Kaynak ve Kesme Fabrikası ve Tedarikçiler (xinfatools.com)
4. Ana proses parametrelerinin analizi
1. Elektrot basıncı. Haddeleme kaynağında elektrotun iş parçasına uyguladığı basınç, kaynağın kalitesini etkileyen önemli bir parametredir. Elektrot basıncı çok düşükse, yerel yüzey yanmasına, taşmasına, yüzey sıçramasına ve aşırı nüfuza neden olur; elektrot basıncı çok yüksekse girinti çok derin olacak ve elektrot silindirinin deformasyonu ve kaybı hızlanacaktır.
2. Kaynak hızı ve darbe frekansı. Kapalı bir rulo kaynağı için kaynak noktaları ne kadar yoğunsa o kadar iyidir. Kaynak noktaları arasındaki örtüşme katsayısı tercihen %30'dur. Kaynak hızının ve darbe frekansının değişmesi, örtüşme oranının değişimini doğrudan etkiler.
3. Şarj kapasitörü ve voltajı. Şarj kondansatörünün veya şarj voltajının değiştirilmesi, kaynak sırasında iş parçasına iletilen enerjiyi değiştirir. İkisinin farklı parametrelerinin eşleştirilmesi yöntemi, güçlü ve zayıf spesifikasyonlar arasındaki farka sahiptir ve farklı malzemeler için farklı enerji spesifikasyonları gereklidir.
4. Makaralı elektrot uç yüzünün şekli ve boyutu. Yaygın olarak kullanılan silindir elektrot formları F tipi, SB tipi, PB tipi ve R tipidir. Makaralı elektrotun uç yüz boyutu uygun olmadığında, kaynak çekirdeğinin boyutunu ve nüfuz etme oranını etkileyecektir ve ayrıca kaynak işlemi üzerinde de belirli bir etkiye sahip olacaktır.
Rulo kaynak bağlantılarının kalite gereklilikleri temel olarak bağlantıların iyi sızdırmazlık ve korozyon direncine yansıdığından, yukarıdaki parametreler belirlenirken nüfuz etme ve örtüşme oranının etkisi dikkate alınmalıdır. Gerçek kaynak prosesinde çeşitli parametreler birbirini etkiler ve yüksek kaliteli rulo kaynak bağlantıları elde etmek için uygun şekilde koordine edilmeli ve ayarlanmalıdır.
Gönderim zamanı: 12 Eylül 2024