Çoğu durumda MIG tabancası sarf malzemeleri, ekipman, iş akışı, parça tasarımı ve daha fazlası ile ilgili kaygılar kaynak operatörlerinin, denetçilerin ve operasyona dahil olan diğer kişilerin dikkatini çektiği için kaynak sürecinde sonradan akla gelen bir düşünce olabilir. Ancak bu bileşenler, özellikle de kontak uçları, kaynak performansı üzerinde önemli bir etkiye sahip olabilir.
MIG kaynak işleminde kontak ucu, kaynak akımını delikten geçerken tele aktararak ark oluşturmaktan sorumludur. Optimal olarak tel, elektrik temasını korurken minimum dirençle beslenmelidir. Temas ucunun nozül içindeki, kontak ucu girintisi olarak adlandırılan konumu da aynı derecede önemlidir. Kaynak işleminde kaliteyi, üretkenliği ve maliyetleri etkileyebilir. Ayrıca, operasyonun genel verimine veya karlılığına katkıda bulunmayan parçaların taşlanması veya patlatılması gibi katma değeri olmayan faaliyetler için harcanan süreyi de etkileyebilir.
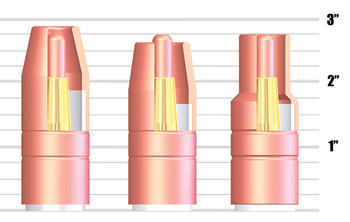
Doğru kontak ucu girintisi uygulamaya göre değişir. Daha az kablo çıkıntısı tipik olarak daha stabil bir ark ve daha iyi düşük voltaj nüfuzu sağladığından, en iyi kablo çıkıntısı uzunluğu genellikle uygulama için izin verilen en kısa olandır.
Kaynak kalitesine etkisi
Temas ucu girintisi, kaynak kalitesini etkileyebilecek bir dizi faktörü etkiler. Örneğin, çıkıntı veya elektrot uzantısı (kontak ucunun ucu ile çalışma yüzeyi arasındaki telin uzunluğu), kontak ucu girintisine göre değişir; özellikle kontak ucu girintisi ne kadar büyük olursa, tel çıkıntısı da o kadar uzun olur. Kablo çıkıntısı arttıkça voltaj artar ve amper düşer. Bu meydana geldiğinde arkın stabilitesi bozulabilir ve aşırı sıçramaya, arkın dolaşmasına, ince metallerde zayıf ısı kontrolüne ve daha yavaş ilerleme hızlarına neden olabilir.
Kontak ucu girintisi aynı zamanda kaynak arkından gelen radyant ısıyı da etkiler. Isı birikmesi, ön uç sarf malzemelerinde elektrik direncinin artmasına neden olur ve bu da kontak ucunun akımı tele aktarma yeteneğini azaltır. Bu zayıf iletkenlik, yetersiz nüfuziyete, sıçramaya ve kabul edilemez bir kaynakla sonuçlanabilecek veya yeniden işleme yol açabilecek diğer sorunlara neden olabilir.
Ayrıca çok fazla ısı genellikle kontak ucunun çalışma ömrünü azaltır. Sonuç, daha yüksek genel sarf malzemesi maliyetleri ve kontak ucu değişimi için daha fazla aksama süresidir. Bir kaynak işleminde işçilik neredeyse her zaman en büyük maliyet olduğundan, bu aksama süresi üretim maliyetlerinde gereksiz artışlara yol açabilir.
Temas ucu girintisinden etkilenen bir diğer önemli faktör koruyucu gaz kapsamıdır. Temas ucunun girintisi memeyi arktan ve kaynak birikintisinden uzağa konumlandırdığında kaynak alanı, koruyucu gazı bozabilecek veya yerini değiştirebilecek hava akışına daha duyarlı hale gelir. Koruyucu gazın zayıf kapsamı gözenekliliğe, sıçramaya ve yetersiz nüfuza yol açar.
Tüm bu nedenlerden dolayı uygulama için doğru temas girintisinin kullanılması önemlidir. Bazı öneriler aşağıdadır.
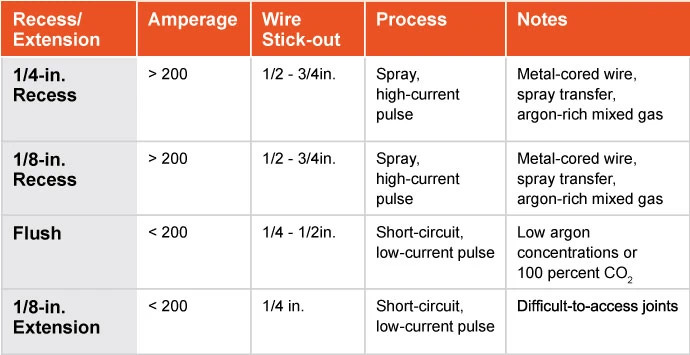
Şekil 1: Doğru kontak ucu girintisi uygulamaya göre değişir. İş için doğru kontak ucu girintisini belirlemek için daima üreticinin tavsiyelerine başvurun.
Temas ucu girintisi türleri
Difüzör, uç ve nozül, MIG tabancası sarf malzemelerini oluşturan üç ana parçadır. Difüzör doğrudan tabanca boynuna bağlanır ve akımı kontak ucuna taşır ve gazı nozüle yönlendirir. Uç difüzöre bağlanır ve akımı nozülden kaynak birikintisine yönlendirirken tele aktarır. Nozül difüzöre bağlanır ve koruyucu gazın kaynak arkına ve su birikintisine odaklanmasını sağlar. Her bileşen genel kaynak kalitesinde kritik bir rol oynar.
MIG tabancası sarf malzemeleriyle iki tip kontak ucu girintisi mevcuttur: sabit veya ayarlanabilir. Ayarlanabilir bir kontak ucu girintisi farklı derinlik ve uzantı aralıklarına göre değiştirilebildiğinden, farklı uygulama ve proseslerin girinti taleplerini karşılayabilme avantajına sahiptirler. Bununla birlikte, kaynak operatörleri bunları nozülün konumunu manevra yaparak veya kontak ucunu belirli bir girintiye sabitleyen bir kilitleme mekanizması aracılığıyla ayarladıkları için insan hatası potansiyelini de arttırırlar.
Değişiklikleri önlemek için bazı şirketler, kaynak homojenliğini sağlamanın ve bir kaynak operatöründen diğerine tutarlı sonuçlar elde etmenin bir yolu olarak sabit girintili uçları tercih ediyor. Sabit girintili uçlar, tutarlı bir uç konumunun kritik olduğu otomatik kaynak uygulamalarında yaygındır.
Farklı üreticiler, genellikle 1⁄4 inç girintiden 1⁄8 inç uzatmaya kadar değişen çeşitli kontak ucu girinti derinliklerine uyacak şekilde sarf malzemeleri üretir.
Doğru girintinin belirlenmesi
Doğru kontak ucu girintisi uygulamaya göre değişir. Çoğu durumda dikkate alınması gereken iyi bir kural, akım arttıkça girintinin de artması gerektiğidir. Ayrıca daha az kablo çıkıntısı tipik olarak daha kararlı bir ark ve daha iyi düşük voltaj nüfuzu sağladığından, en iyi kablo çıkıntısı uzunluğu genellikle uygulama için izin verilen en kısa olandır. Aşağıda bazı yönergeleri bulabilirsiniz. Ayrıca ek notlar için Şekil 1'e bakın.
1. Darbeli kaynak, püskürtme transfer işlemleri ve 200 amperden büyük diğer uygulamalar için 1/8 inç veya 1/4 inçlik bir kontak ucu girintisi önerilir.
2. Kalın metallerin geniş çaplı tel veya metal özlü tel ile sprey transfer işlemiyle birleştirilmesi gibi daha yüksek akımlara sahip uygulamalar için, girintili bir kontak ucu, kontak ucunun arkın yüksek ısısından uzak tutulmasına da yardımcı olabilir. Bu işlemler için daha uzun bir tel çıkıntısının kullanılması, geri yanma (telin eriyip kontak ucuna yapışması) ve sıçrama oluşumunu azaltmaya yardımcı olur, bu da kontak ucunun ömrünün uzatılmasına ve sarf malzemesi maliyetlerinin azaltılmasına yardımcı olur.
3. Kısa devre transfer işlemi veya düşük akımlı darbe kaynağı kullanıldığında, genellikle yaklaşık 1⁄4 inç tel çıkıntılı bir gömme kontak ucu önerilir. Nispeten kısa çıkıntı uzunluğu, yanma veya bükülme riski olmadan ve düşük sıçramayla ince malzemelerin kaynaklanması için kısa devre aktarımına olanak tanır.
4. Uzatılmış kontak uçları genellikle boru kaynağındaki derin ve dar V-oluk bağlantıları gibi erişilmesi zor bağlantı konfigürasyonlarına sahip çok sınırlı sayıda kısa devre uygulaması için ayrılmıştır.
Bu hususlar seçim konusunda yardımcı olabilir ancak iş için doğru kontak ucu girintisini belirlemek için daima üreticinin tavsiyelerine başvurun. Doğru konumun aşırı sıçrama, gözeneklilik, yetersiz nüfuz etme, yanma veya daha ince malzemelerde bükülme ve daha fazlası olasılığını azaltabileceğini unutmayın. Üstelik bir şirket, bu tür sorunların sorumlusunun kontak ucu girintisi olduğunu anladığında, zaman alıcı ve maliyetli sorun giderme veya yeniden işleme gibi kaynak sonrası faaliyetlerin ortadan kaldırılmasına yardımcı olabilir.
Ek bilgi: Kaliteli ipuçlarını seçin
Temas uçları kaliteli kaynakların tamamlanmasında ve aksama süresinin azaltılmasında önemli bir faktör olduğundan, yüksek kaliteli bir temas ucunun seçilmesi önemlidir. Bu ürünler daha düşük kalitedeki ürünlerden biraz daha pahalı olsa da, kullanım ömrünü uzatarak ve değişim nedeniyle arıza süresini azaltarak uzun vadeli değer sunarlar. Ek olarak, daha yüksek kaliteli kontak uçları geliştirilmiş bakır alaşımlarından yapılabilir ve genellikle daha sıkı mekanik toleranslara göre işlenir; böylece ısı birikimini ve elektrik direncini en aza indirmek için daha iyi bir termal ve elektrik bağlantısı oluşturulur. Daha yüksek kaliteli sarf malzemeleri genellikle daha pürüzsüz bir merkez deliğine sahiptir, bu da telin içinden geçerken daha az sürtünmeye neden olur. Bu, daha az sürtünme ve daha az potansiyel kalite sorunuyla tutarlı tel besleme anlamına gelir. Daha yüksek kaliteli kontak uçları aynı zamanda geri yanmaların en aza indirilmesine ve tutarsız elektrik iletkenliğinin neden olduğu düzensiz arkın önlenmesine de yardımcı olabilir.
Gönderim zamanı: Ocak-01-2023