Gözeneklilik, katılaşma sırasında gaz sıkışmasıyla oluşan boşluk tipi süreksizlikler, MIG kaynağında yaygın fakat külfetli bir kusurdur ve birkaç nedeni vardır.Yarı otomatik veya robotik uygulamalarda görünebilir ve her iki durumda da çıkarılması ve yeniden işlenmesi gerekir; bu da arıza sürelerine ve artan maliyetlere yol açar.
Çelik kaynağındaki gözenekliliğin ana nedeni, kaynak havuzuna karışan nitrojendir (N2).Sıvı havuzu soğuduğunda, N2'nin çözünürlüğü önemli ölçüde azalır ve N2, kabarcıklar (gözenekler) oluşturarak erimiş çelikten dışarı çıkar.Galvaniz/galvanik kaynakta, buharlaşan çinko kaynak havuzuna karışabilir ve havuz katılaşmadan kaçmak için yeterli zaman yoksa gözenek oluşturur.Alüminyum kaynağı için, tüm gözenekliliğe hidrojen (H2) neden olur, aynı şekilde N2 çelikte çalışır.
Kaynak gözenekliliği harici veya dahili olarak görünebilir (genellikle alt yüzey gözenekliliği olarak adlandırılır).Ayrıca kaynak üzerinde tek bir noktada veya tüm uzunluk boyunca gelişerek zayıf kaynaklara neden olabilir.
Gözenekliliğin bazı temel nedenlerinin nasıl belirleneceğini ve bunların nasıl hızla çözüleceğini bilmek kaliteyi, üretkenliği ve kârlılığı artırmaya yardımcı olabilir.
Yetersiz Koruyucu Gaz Kapsamı
Zayıf koruyucu gaz kapsamı, atmosferik gazların (N2 ve H2) kaynak havuzunu kirletmesine izin verdiği için kaynak gözenekliliğinin en yaygın nedenidir.Yetersiz koruyucu gaz akış hızı, gaz kanalındaki sızıntılar veya kaynak hücresinde çok fazla hava akışı dahil ancak bunlarla sınırlı olmamak üzere çeşitli nedenlerle uygun kaplama eksikliği meydana gelebilir.Çok yüksek seyahat hızları da bir suçlu olabilir.
Operatör soruna zayıf akışın neden olduğundan şüpheleniyorsa, hızın yeterli olduğundan emin olmak için gaz akış ölçeri ayarlamayı deneyin.Örneğin, bir sprey transfer modunu kullanırken, saatte 35 ila 50 fit küp (cfh) akış yeterli olacaktır.Daha yüksek amperlerde kaynak yapmak, akış hızında bir artış gerektirir, ancak hızı çok yüksek ayarlamamak önemlidir.Bu, koruyucu gaz kapsamını bozan bazı tabanca tasarımlarında türbülansa neden olabilir.
Farklı tasarlanmış tabancaların farklı gaz akışı özelliklerine sahip olduğuna dikkat etmek önemlidir (aşağıdaki iki örneğe bakın).Üst tasarım için gaz akış hızının "tatlı noktası", alt tasarımdan çok daha büyüktür.Bu, kaynak hücresini ayarlarken bir kaynak mühendisinin dikkate alması gereken bir şeydir.
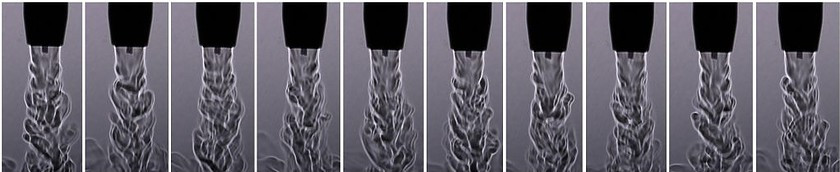
Tasarım 1, meme çıkışında düzgün gaz akışını gösterir
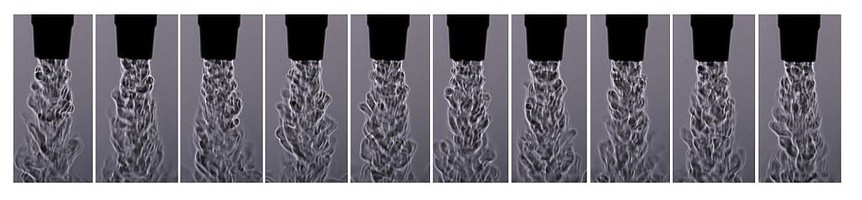
Tasarım 2, meme çıkışındaki türbülanslı gaz akışını göstermektedir.
Ayrıca gaz hortumunda, bağlantı parçalarında ve konektörlerde ve ayrıca MIG kaynak tabancasının güç pimindeki O-ringlerde hasar olup olmadığını kontrol edin.Gerekirse değiştirin.
Bir kaynak hücresindeki operatörleri veya parçaları soğutmak için fanlar kullanırken, gaz kapsamını bozabilecekleri şekilde doğrudan kaynak alanına doğrultulmamasına dikkat edin.Harici hava akışından korumak için kaynak hücresine bir ekran yerleştirin.
İstenen ark uzunluğuna bağlı olarak tipik olarak ½ ila 3/4 inç olan uygun bir uç-çalışma mesafesi olduğundan emin olmak için robotik uygulamalarda programa yeniden dokunun.
Son olarak, gözeneklilik devam ederse seyir hızlarını düşürün veya daha iyi gaz kapsamına sahip farklı ön uç bileşenleri için bir MIG tabanca tedarikçisine danışın.
Baz Metal Kirliliği
Baz metal kirlenmesi, yağ ve gresten hadde tufalına ve pasa kadar gözenekliliğin ortaya çıkmasının başka bir nedenidir.Nem, özellikle alüminyum kaynağında bu süreksizliği de teşvik edebilir.Bu tür kirleticiler tipik olarak operatör tarafından görülebilen dış gözenekliliğe yol açar.Galvanizli çelik, yüzey altı gözenekliliğine daha yatkındır.
Dış gözeneklerle mücadele etmek için, kaynak yapmadan önce taban malzemesini iyice temizlediğinizden emin olun ve metal özlü bir kaynak teli kullanmayı düşünün.Bu tür tel, katı telden daha yüksek seviyelerde oksit gidericilere sahiptir, bu nedenle temel malzeme üzerinde kalan kirletici maddelere karşı daha toleranslıdır.Bunları ve diğer telleri her zaman tesise benzer veya biraz daha yüksek sıcaklıktaki kuru, temiz bir alanda saklayın.Bunu yapmak, kaynak havuzuna nem getirebilecek ve gözenekliliğe neden olabilecek yoğuşmayı en aza indirmeye yardımcı olacaktır.Kabloları soğuk bir depoda veya açık havada saklamayın.
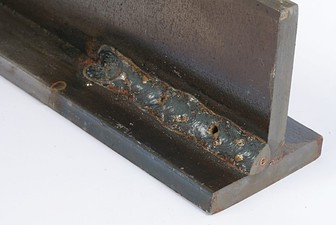
Gözeneklilik, katılaşma sırasında gaz sıkışmasıyla oluşan boşluk tipi süreksizlikler, MIG kaynağında yaygın fakat külfetli bir kusurdur ve birkaç nedeni vardır.
Galvanizli çeliği kaynak yaparken, çinko çeliğin erimesinden daha düşük bir sıcaklıkta buharlaşır ve hızlı ilerleme hızları kaynak havuzunun hızla donmasına neden olur.Bu, çelikte çinko buharını hapsederek gözenekliliğe neden olabilir.Seyir hızlarını izleyerek bu durumla mücadele edin.Yine, kaynak havuzundan çinko buharının kaçmasını destekleyen özel olarak tasarlanmış (akı formülü) metal özlü teli göz önünde bulundurun.
Tıkalı ve/veya Küçük Nozüller
Tıkalı ve/veya normalden küçük püskürtme uçları da gözenekliliğe neden olabilir.Nozülde ve temas memesinin ve difüzörün yüzeyinde kaynak sıçraması birikerek koruyucu gaz akışının kısıtlanmasına veya türbülanslı hale gelmesine neden olabilir.Her iki durum da kaynak havuzunu yetersiz korumayla terk eder.
Bu durumu oluşturan, uygulama için çok küçük olan ve daha fazla ve daha hızlı sıçrama oluşumuna daha yatkın olan bir nozüldür.Daha küçük nozullar daha iyi bağlantı erişimi sağlayabilir, ancak aynı zamanda gaz akışı için izin verilen daha küçük kesit alanı nedeniyle gaz akışını da engeller.Meme seçiminizle koruyucu gaz akışını ve gözenekliliği etkileyen başka bir faktör olabileceğinden, temas ucunun meme çıkıntısına (veya girintisine) değişkenini daima aklınızda bulundurun.
Bunu göz önünde bulundurarak, nozulun uygulama için yeterince büyük olduğundan emin olun.Tipik olarak, daha büyük tel boyutları kullanan yüksek kaynak akımına sahip uygulamalar, daha büyük delik boyutlarına sahip bir meme gerektirir.
Yarı otomatik kaynak uygulamalarında, memedeki kaynak çapaklarını periyodik olarak kontrol edin ve kaynakçı pensesi (kaynakçı) kullanarak giderin veya gerekirse memeyi değiştirin.Bu inceleme sırasında kontak ucunun iyi durumda olduğunu ve gaz difüzörünün açık gaz portlarına sahip olduğunu doğrulayın.Operatörler ayrıca sıçrama önleyici bileşik kullanabilirler, ancak aşırı miktarda bileşik koruyucu gazı kirletebileceğinden ve meme yalıtımına zarar verebileceğinden, memeyi bileşiğe çok fazla veya çok uzun süre daldırmamaya özen göstermelidirler.
Bir robotik kaynak işleminde, sıçrama oluşumuyla mücadele etmek için bir meme temizleme istasyonuna veya raybaya yatırım yapın.Bu çevre birimi, üretimdeki rutin duraklamalarda nozulu ve difüzörü temizler, böylece döngü süresini etkilemez.Meme temizleme istasyonları, ön bileşenlere ince bir kat bileşik uygulayan sıçrama önleyici bir püskürtücü ile birlikte çalışacak şekilde tasarlanmıştır.Sıçrama önleyici sıvının çok fazla veya çok az olması ek gözenekliliğe neden olabilir.Nozül temizleme işlemine hava üfleme eklemek, sarf malzemelerinden gevşek sıçramaların temizlenmesine de yardımcı olabilir.
Kalite ve üretkenliği sürdürmek
Kaynak sürecini izlemeye özen göstererek ve gözenekliliğin nedenlerini bilerek, çözümleri uygulamak nispeten kolaydır.Bunu yapmak, daha uzun ark süresi, kaliteli sonuçlar ve üretim boyunca hareket eden daha iyi parçalar sağlamaya yardımcı olabilir.
Gönderim zamanı: Şubat-02-2020